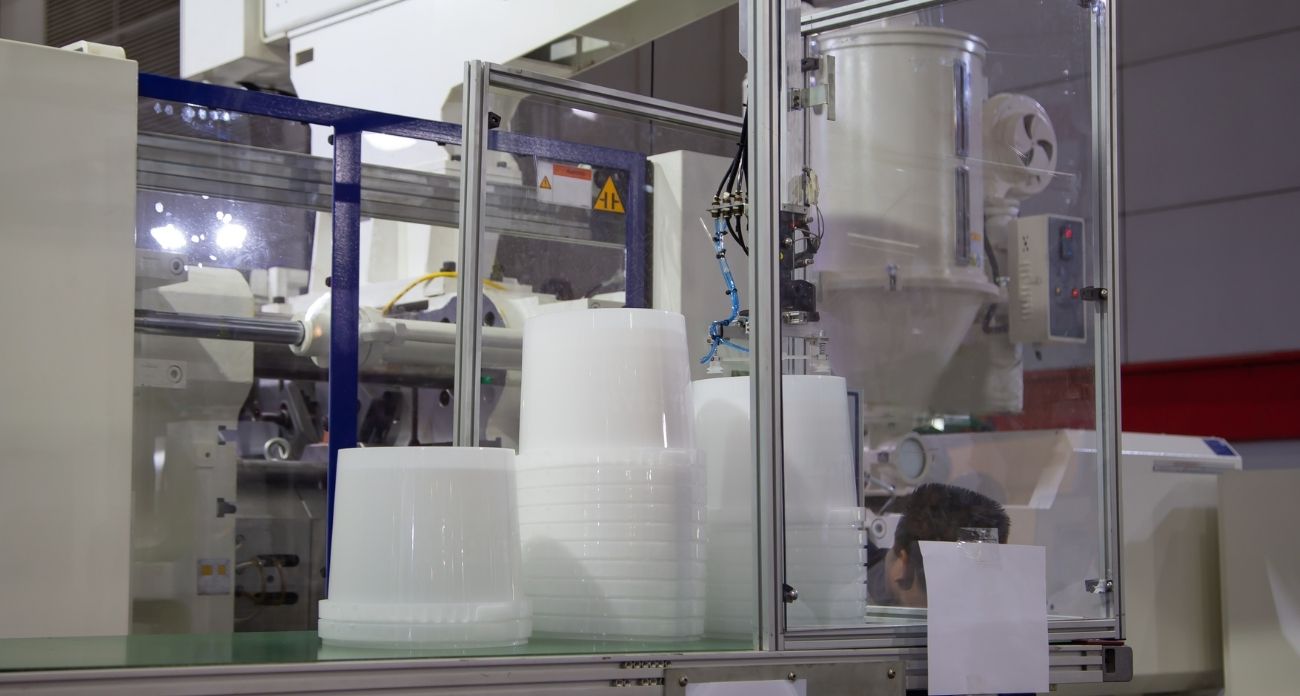
What is Injection Mold Design?
Injection molds are products made of durable and hard metals such as stainless steel, steel or aluminum and can be reused for many years. Injection mold design is one of the most common types of molding used today for both consumer products and engineering applications. Almost every plastic product you see around is produced using injection molding. The reason for this is related to the production of the same parts in very high volumes with the cost per part of the technology. However, the initial costs of injection molding processes are high, as special tooling molds are needed. Nevertheless, the serial production stages of the part after the design are largely sufficient to cover the initial costs and even more.
How to Design an Injection Mold?
While designing an injection mold, there are costs such as mold materials (steel or aluminum), accuracy tests (prototype studies, full-scale production molds), and the complexity of the geometric structure of the mold. The injection molding method accounts for more than 40% of all plastic parts produced on a global basis each year. Before starting the mold design, the material of the part is selected, the production methods are determined, and the 3D geometry and tolerance technical drawing of the part product to be produced is drawn. The number of chambers of the mold is determined within the information such as monthly production, production information, investment budget and cycle time. The principles of injection mold such as cooling principles, runner and pusher types are determined respectively. After understanding the basic principles of the mold and taking orders, detailed designs of the mold can be started. The movement sequence, working principle and steps of mold designs made in 3D can be analyzed. After the mold designs are finished, the materials are ordered and mold production is started. The process becomes ready by completing the mold trial, and approval of the mold and the part, in the final process.
Injection Mold Design Advantages and Disadvantages
Injection molding is a well-established production technology with a long history.
It is a type of molding that constantly develops and improves its existence with new technological developments. However, this type of molding has some advantages and disadvantages.
Injection Mold Design Advantages:
- It provides high-volume plastic production.
- Thanks to its wide material range, it offers a variety of materials with different physical properties.
- With high productivity, a single mold accommodates multiple parts and this phase can further increase production processes and capacities.
- This type of molding can be repeated quite a lot.
- Products that do not require finishing can be produced with a perfect visual appearance.
Injection Mold Design Disadvantages:
- The main economic limitation of this type of molding is the high initial costs for the tooling. Making a special mold for each geometry part increases the initial costs.
- Design changes after a mold has been produced are quite costly.
- Delivery times can sometimes take longer than necessary.
For detailed information about IML, you can contact the MoldMore expert team.