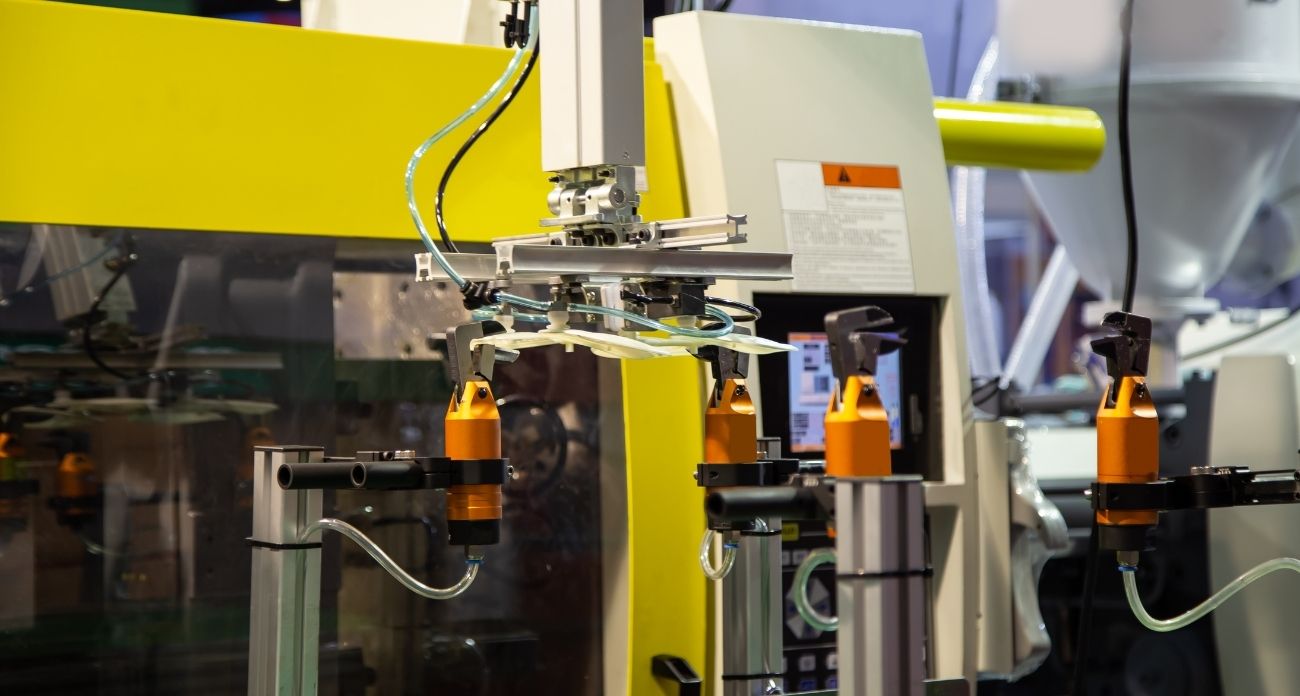
Hot Runner Systems in Plastic Injection Molds
One of the methods used for shaping plastic material is plastic injection molds. These molds allow the plastic material to be shaped in the mold by melting it under high temperatures. Thanks to plastic injection molds, the size, shape and quality of the product in question are determined through molds. The hot runner system, which is frequently used in the injection molding method, is an important process step.
What is Hot Runner System for Plastic Injection Mold?
There are two runner systems used in the plastic injection production phase. These are the hot runner and cold runner systems. These runner systems refer to all the systems through which the molten plastic material passes as it moves into the mold cavity. To ensure production efficiency, runner systems are selected in a way that will positively affect the quality of the product.
The main purpose of the runner system is to provide the flow of plastic material to the mold chamber. Hot runner systems, on the other hand, inject the material into the mold cavity as desired by maintaining the current temperature without pressure loss. The hot runner system is located inside the plastic injection mold. The material that gives heat to the plastic product in this way is resistance. Resistors, as a material in the hot runner system, fulfill the task of giving heat as desired. Thus, a controlled process that affects product quality is realized. The advantages of the hot runner system that affect the product quality attract the attention of most injection molding companies.
What are the Advantages of the Hot Runner System?
The hot runner system is preferred to the cold runner system, which is another runner. This is because it offers a short-term production process that affects the quality of the plastic product. Through hot runner systems, it is possible to do more work in a short time. In general, the advantages of hot runner systems in injection molds are as follows:
- Preventing possible heat losses,
- Performing short-term labor in a way that can save time,
- Ensuring that the product is handled in a controlled manner without causing product quality problems,
- Increasing production efficiency by adapting to the automation system,
- Ability to print unprintable materials with the cold runner system.
Apart from the advantages of hot runner systems, there is also a shortcoming that should not be overlooked. Hot runners can cause a burning problem and an expansion problem on the part surface if necessary precautions are not taken in the system design. To prevent such situations, it is necessary to choose a hot runner system that is specially designed for the usage area and various precautions are taken.
We tried to convey to you the two most important concepts of the plastics industry. If you want to get detailed information about specially designed injection molds in plastic production, you can contact the MoldMore expert team.