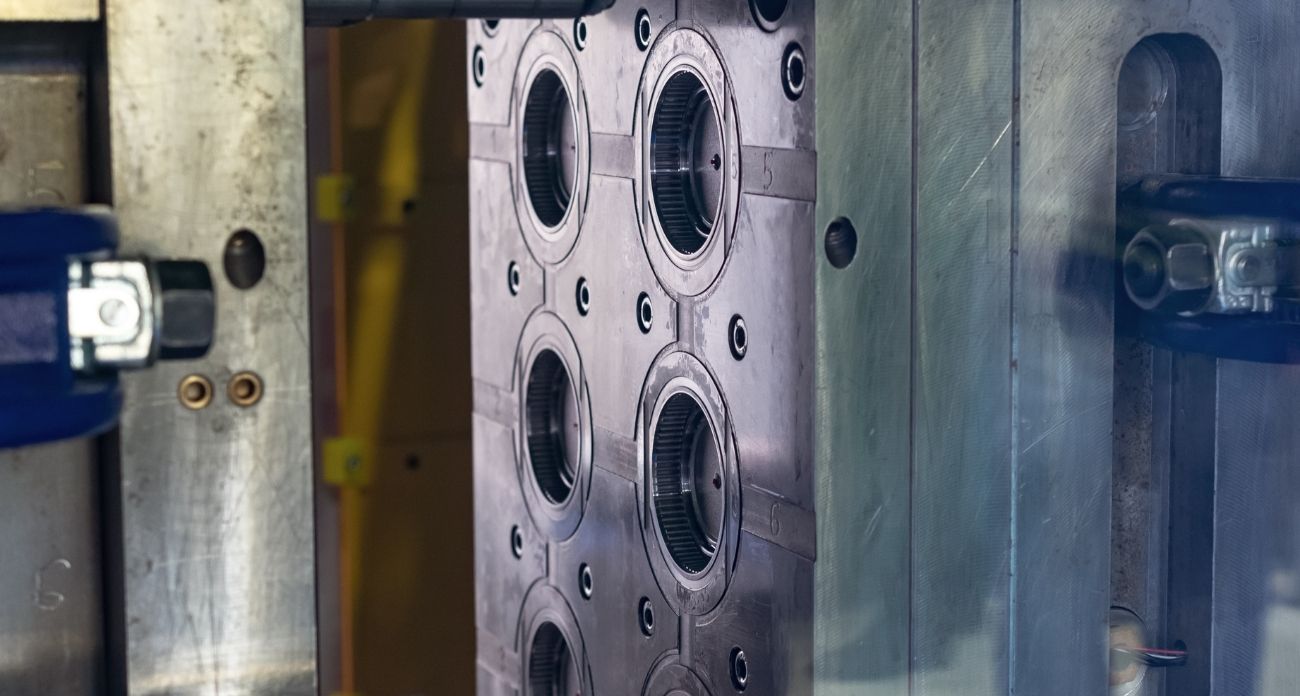
Where are Plastic Injection Molds Used?
Plastic injection molds are tools used to produce large quantities of plastic products. For the plastic melted in injection machines to take the shape of the product, they need plastic injection molds in suitable forms. After their designs are completed, the molds must be manufactured with the help of high-precision CNC machines.
Plastic Injection Mold Usage Areas:
- White goods industry,
- Home electronics industry,
- Decoration and furniture industry,
- Automotive industry,
- Hardware and hand tools industry,
- Water treatment industry,
- Stationery industry,
- Medical sector,
- Toy industry,
- Air conditioning industry,
- Glassware industry,
- Machinery manufacturing (marble, cable, etc.) industry.
What are the Products Produced with Plastic Injection Molds?
Water is sprayed into the molds connected to the plastic injection machine and the mold is filled and the plastic parts are taken out within a certain time. For the molds to take certain shapes, the properties of plastic materials and their behavior in the mold must be known. There are three steps in the production of the plastic injection molding process.
Three Basic Steps in the Plastic Injection Molding Process:
- Product design,
- Production control,
- Quality control.
It is necessary to determine the costs of the plastic parts in these three basic processes. Quality controls are carried out both during and after production. The quality is kept at a certain level if the designed products are checked whether they comply with the determined standards. The design of the product and its production processes are the most basic processes to be considered in determining the costs of plastic parts. Products produced with plastic injection molds include automotive bumpers, instrument panels, electrical switches, CDs, technological systems, and medical supplies in the health sector.
Why Choose Plastic Injection Molds?
There are multiple reasons to choose injection molding in plastic production. First, injection molding provides absolute accuracy with the consistency of the properties of the materials used. It is done quickly, efficiently and with high precision in the processing of prototypes of mixed shapes. Another important reason is that the improved resistance and flexibility of the products in post-mold processes are superior. Injection machines give accurate results when combined with high-resistance components. Due to its minimal loss rates, it can be reproduced quickly. Thanks to these advantages, it takes its place among the most popular methods. Unlike plastic processing in long-term injection processes, it saves a lot of costs.
For detailed information about IML, you can contact the MoldMore expert team.